交付周期从6个月到50天,联泰科技助力汽车产业柔性化智能变革
美国斯丹迪斯Standex国际集团(下称模德模具)成立于1955年,是全球最早将蚀纹成功应用在产品上的企业之一,旗下拥有食品服务设备集团、工程技术集团、电子集团、液压集团、雕刻集团5大集团公司。其中,雕刻集团在全球分布35家工厂,在中国有7家纹理雕刻工厂。工厂实行就近原则,并提供配套的技术支持,旨在为全球客户带来DVP一站式蚀纹服务。

“模德模具与联泰科技的合作开始于2019年,我们首次购入了联泰科技旗下工业级大幅面3D打印机G1800。在3D打印技术的助力下,模德模具的生产周期、生产成本及产品质量实现了大幅提升,同时也完成了企业的数字化智能转型。模德模具与联泰科技的深度合作不仅仅是双方企业的互利互惠,更是增材制造与汽车行业的同频共振。”
——斯丹迪斯模德亚太区销售副总裁
模德苏州总经理 吴涛
22年前,模德模具首次进入中国市场。依托汽车行业的蓬勃发展,最初主要做一些生产型任务。伴随着3D打印技术的兴起,其业务类型也由最初的纹理加工服务慢慢拓展至纹理设计、验证服务等。2019年,模德模具首次引进联泰科技工业级光固化3D打印机G1800,并依托3D打印技术开启了汽车产业的柔性化智能变革。
联泰科技工业级大幅面3D打印机—G1800

G1800采用1800×900×600
mm的超大幅面设计,配合联泰科技自主研发的碳纤维涂敷刮刀系统,其独特的上下运行打印路径,相较于市面上的左右运行,显著缩短了刮刀的来回运动里程,助力打印速度再次进阶的同时,有效实现了材料的循环利用。这一独创优势推动了工业生产的降本、提质、增效,让生产过程更节能、更环保,在多个行业的模型制造中发挥着重要作用。

G1800拥有国内首创的拼接扫描算法,将相邻振镜扫描的同一个成型件的两侧部位无缝拼接在一起,增加了两侧区域的接触面积,从而保证成型件在拼接区域卓越的力学性能。这一独创的“交叉拼接”技术,既能保证成型件在拼接区域的表面质量,又可保证拼接区域的力学性能,基本接近同一振镜独立扫描成型的制件的力学性能(90%以上),使得多激光高效生产下的模型质量和稳定性再次进阶。

模德模具表示,3D打印技术的融入加速了产品的开发周期。面对传统油泥模型的测试,整个前期工作的周期大概需要6个月甚至1年,才能形成油泥模型的一个验证;而3D打印技术的加入可快速实现尺寸、色彩甚至内部纹理结构数据的验证。在3D打印技术的加持下,其项目预估交付周期从传统的6个月缩短至实际交付50天。配合其自主研发的smart
skin,使得纹理的延展性和触感更佳,进而实现了交期及品质上的双项提升。
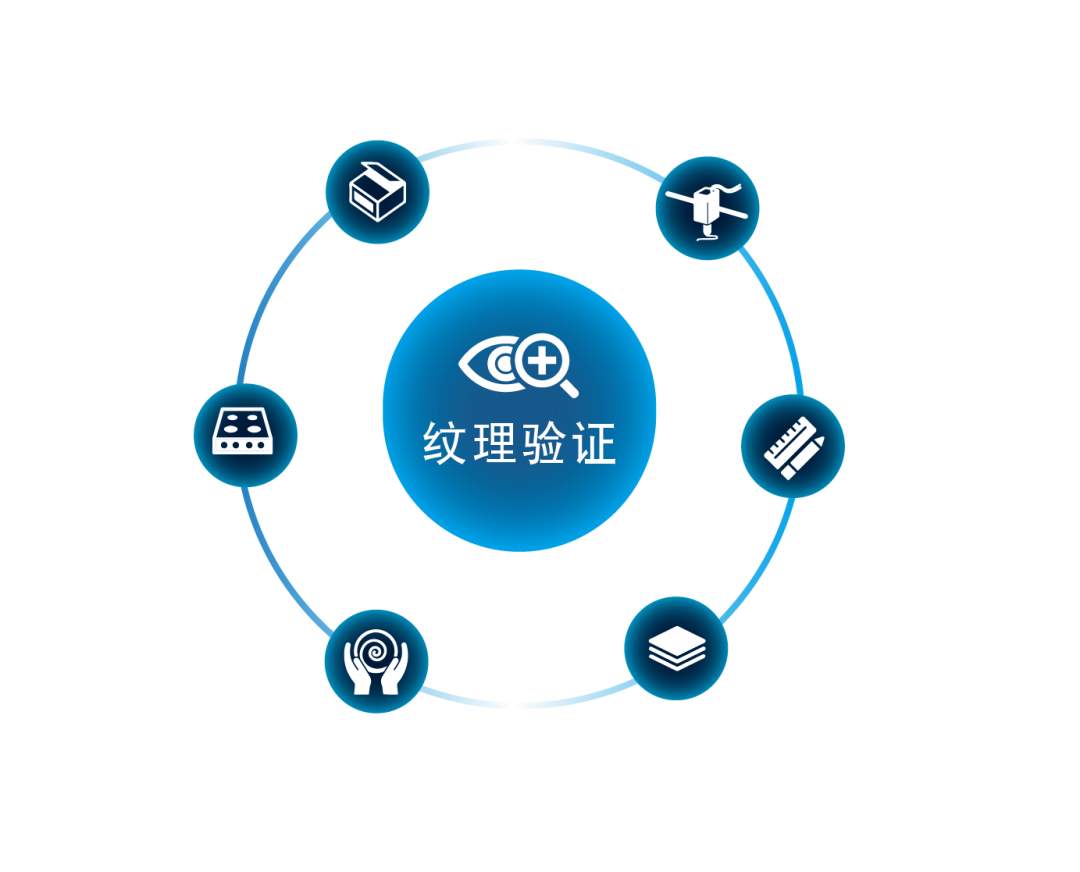
伴随着金属3D打印技术的日益成熟,其在汽车领域的应用也变得更加普遍。在功能纹理应用的研发过程中,“极致的纹理复制要求”是模德模具不可避免的一大挑战。功能纹理对注塑、模具、产品加工的要求远超普通纹理,而金属3D打印的融入对功能纹理研发产生了极大地赋能。例如在模具验证阶段,金属3D打印能够更好地去设计冷却、加热水道,配合模德模具自身技术优势,可实现流道的快速抛光;在表面处理测试中,3D打印能够精确还原功能纹理的复杂结构,使纹理细节更精准。且经测试发现,金属3D打印技术能够满足铣削和加工的要求及电磁加热等应用。目前,模德模具已成功运用金属3D打印技术来赋能功能纹理的开发。其中光学微结构、光学防眩晕纹理等多种功能纹理已成功面向市场并快速流通。


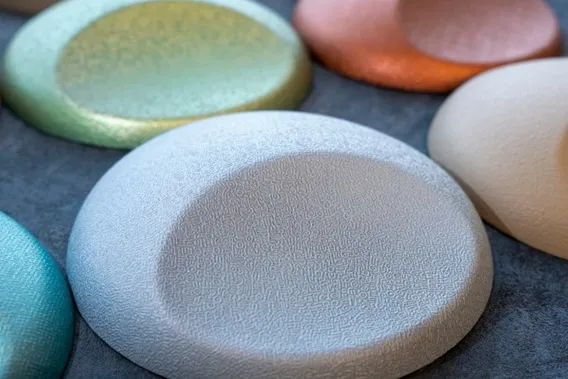


金属3D打印技术在汽车行业的应用可细分为生产领域应用、部件领域应用、维修领域应用、研发领域应用等几大维度,这一技术的融入有效提升了研发速度、降低了生产成本,同时促进了汽车行业的全面创新。针对金属3D打印领域,联泰科技也早已展开深度布局,旗下拥有Muees系列以及针对鞋模行业研发的Fuees系列等多款工业级金属3D打印设备,配合自研的智能软件Muees
ONE,能够为用户带来成熟且完善的金属3D打印行业应用解决方案。

Muees310 & Muees430 技术参数
Muees310
成型范围;310x310X400mm(不含基板厚度)
成型仓尺寸:325X325X440mm
打印精度:L<100:±0.1 L≥100:±0.1%XL
打印层厚:0.02-0.1mm
机器尺寸:2885X1405X2280(含循环机)
机器重量:2300KG(含循环机模块)
适配材料:不锈钢、铝合金、模具钢、钛合金、高温合金
Muees430
成型范围;430X340X400mm(不含基板厚度)
成型仓尺寸:440X350X440mm
打印精度:L<100:±0.1 L≥100:±0.1%XL
打印层厚:0.02-0.1mm
机器尺寸:2950X1350X2200(含循环机)
机器重量:2200KG(含循环机模块)
适配材料:不锈钢、铝合金、模具钢、钛合金、高温合金
金属3D打印技术在汽车领域的应用
生产领域应用
世界上第一辆由3D打印制作而成的汽车在2010年诞生于美国,是一款由电池和汽油驱动的三轮混合动力汽车。这辆3D打印而成的汽车在生产周期、生产工序上均优于传统工艺。同时对于汽车款式、机械结构的调整均可通过更改相关3D打印参数进行实现,从而获得现有汽车无法满足的新车型。基于3D打印对复杂结构的高度还原,其在汽车生产领域得到广泛使用。

部件领域应用
除了整车制造,3D打印技术对于汽车零部件的生产更是游刃有余。尤其是金属3D打印技术的融入,进一步满足了汽车领域中对材料有着硬性要求且结构复杂度较高的零部件的制作。同时汽车零部件样机开发量较大,常规的样机开发周期无法满足当下高速迭代的市场需求。而金属3D打印技术的应用成功攻克这一难题,为汽车行业的迭代升级提供了不竭动力。
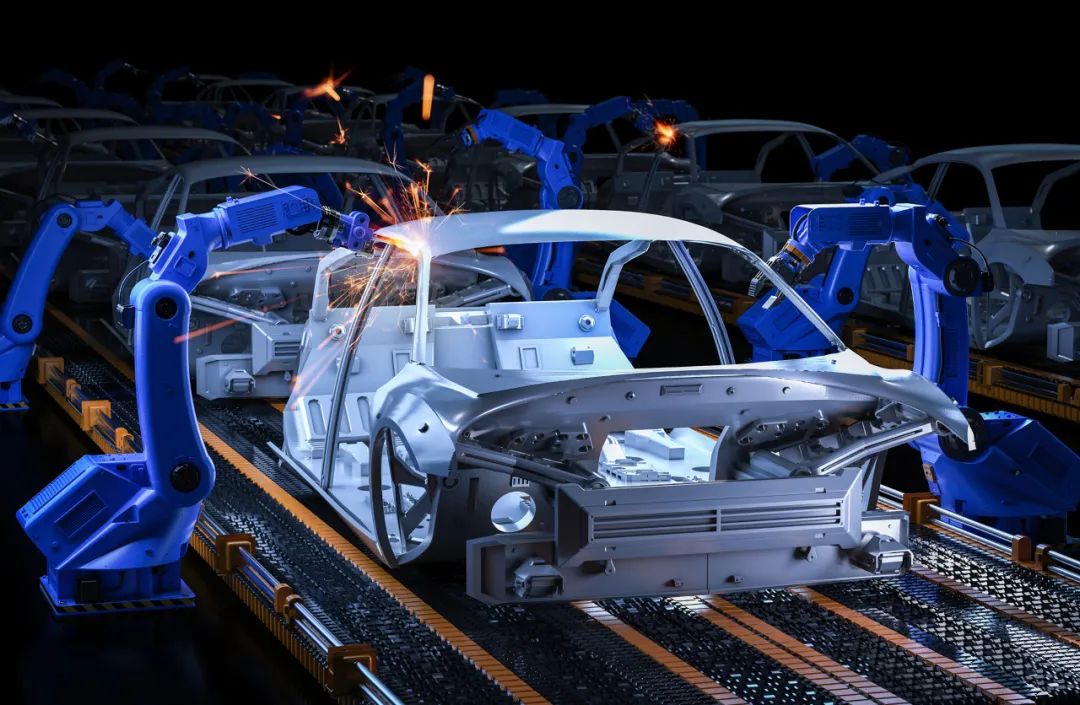
维修领域应用
对于汽车部件的损坏,传统的修复方法造价成本较高且修复效果不理想;重新制造的周期冗长,花费也高昂。而利用金属3D打印技术可以针对损坏部位进行一比一的精准修复,即使是重新制作,整体效率及成果也要优于传统工艺。由此可见,3D打印技术的应用有效降低了汽车维修的难度及成本,同时也最大程度的缓和了备件库存的压力。

研发领域应用
由于3D打印技术对于各类复杂结构的设计拥有绝对的优势,因此工程师在汽车研发阶段可以充分发散自身想象力,在保证高度还原自身设计创意的同时还可以利用这一技术进行研发及制作成本的节约。
金属3D打印技术在汽车领域的优势
轻量化与复杂结构制造
金属3D打印通过一体化成型技术,能够生产传统工艺难以实现的复杂几何结构(如蜂窝状、空心流道),显著降低零部件重量。例如,兰博基尼使用该技术制造轻量化外观件,宝马通过增材制造技术优化部件强度与重量平衡。

缩短研发周期与降低成本
在汽车研发阶段,3D打印无需模具即可快速制作原型和功能性测试件,本田通过引入该技术将原型开发时间大幅缩短,减少外包沟通成本,且材料成本的下降也助力该技术的规模化应用。

定制化生产与维修效率提升
针对高端车型或停产车型,3D打印可按需生产定制部件或修复零件。例如,保时捷Carrera气缸盖的修复通过扫描原部件后直接打印,解决了传统备件停产难题。此外,该技术还可用于现场快速维修,降低库存压力。
在3D打印技术的加持下,汽车行业的柔性化智能生产主要表现为多品类,小批量、个性化的灵活响应,进而帮助企业快速把握市场风向的变化。除蚀纹服务外,这种柔性生产的优势也开拓了汽车行业其他应用场景,如汽车零部件制造、轻量化设计、定制化应用、轮胎模具制造等。其中,成立于2013年的山东力创模具有限公司,在联泰科技数字化3D打印解决方案的助力下,成功实现了轮胎模具生产的智能化变革。
3D打印在汽车行业的应用展示








“3D打印技术通过“设计即制造”的特性,彻底打破了传统工艺对复杂结构的限制,成为了推动行业创新与可持续发展的核心驱动力。未来,在前沿技术的加持下,汽车零部件的拓扑优化及一体化设计将成为常态,并实现全产业链协同赋能的规模化生产。”
—— 联泰科技副总经理
营销中心总经理 汪超
随着汽车行业规模的扩大,3D打印技术的综合生产优势逐步显现,制造的智能化、柔性化、绿色化特征也日益突出。3D打印技术正在突破成本与规模化生产的瓶颈,逐步从汽车研发和高端定制向批量制造渗透。通过材料创新、国产化替代及工艺成熟,未来十年该技术有望成为汽车轻量化、智能化和个性化制造的核心驱动力之一,这种趋势为行业的蓬勃发展带来了充沛的底气及宝贵的契机。
如今,模德模具依托技术支持,面向功能性纹理展开深入研究,并不断加强3D打印技术在汽车行业中的应用,以期带给客户更完善、更前沿的一站式服务体系。后续,联泰科技也将不断加强技术的创新迭代以适应分散化、碎片化、多元化的市场需求,让增材制造技术为更多细分行业带来颠覆性的智能变革。
版权声明
本站部分文章来源于网络,如有侵权请联系删除!。
文章观点并不代表本站观点,请谨慎对待。
发表评论:
◎欢迎参与讨论,请在这里发表您的看法、交流您的观点。